Managing inventory is, most times, oversimplified in businesses.
Is it just a matter of tracking inventory movement?
How many came in, how many were shipped out?
Not quite.
Inventory management is much more than just that.
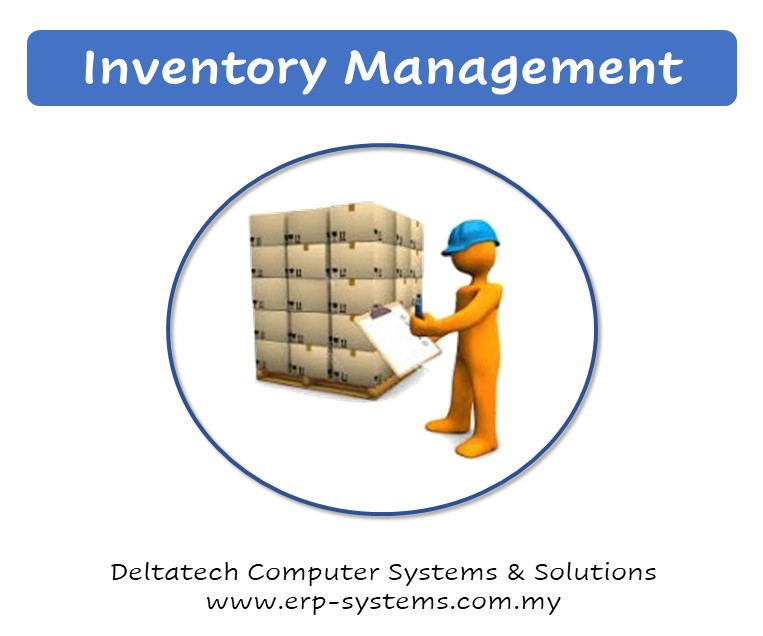
While the basis of inventory management is about tracking movement, it also affects a whole range of other functions that ultimately contribute to the profitability and sustainability of business.
Purchasing
Purchasing relies very much on inventory data to decide on what to buy as well as how much to buy.
Inventory provides the necessary information when making purchasing decisions such as:
- What needs re-ordering
- What quantity to purchase
- What is selling and what is not? (this affects both points 1 and 2 above)
- What was the last purchase price?
- Who are the usual suppliers you purchase from?
- Is there an alternate product?
Sales
In terms of sales on the other hand, inventory management provides information such as:
- What is available?
- If you have multiple inventory locations, is it available elsewhere?
- If stock is not available, when will it be available? In other words, has it been ordered from the supplier and when will it be delivered?
Order processing
When a product is sold, is the process of shipping it out efficient?
To ship it out, you need to know:
- Where is the product located?
- Is there more than 1 order for that product? If there is more than one, can all orders be consolidated so that picking needs to be done only once?
Inventory Control and Management is an important part of the Supply Chain.
Ensuring proper management and control of inventory is critical to managing costs while ensuring you meet customer demand and expectations.
Read how your business your business can benefit from putting in place the right inventory solution.
Articles
- As a business grows
- Is your accounting software doing enough?
- Key benefits of having the right solution to inventory management
- Unified solutions for better management
- Collaborate internally
- Multi Company Management
- Sage Reveals Malaysian Businesses Incur RM56.6 Billion Losses In Productivity A Year
- Mitigating Supply Chain Disruption
- Inventory costing methods
- Sage Wins Two Frost & Sullivan Asia Pacific Awards
- Procure to pay
- Going digital
- What is an ERP system?
- Covid 19 Surviving the coronavirus crisis
- Covid 19 pandemic – Lessons we have learnt