If there’s one thing that comes to mind during this crisis, it should be about supply chain management.
There are so many industries that have been impacted by this pandemic, not because of the lock down, but because their supply chain was disrupted.
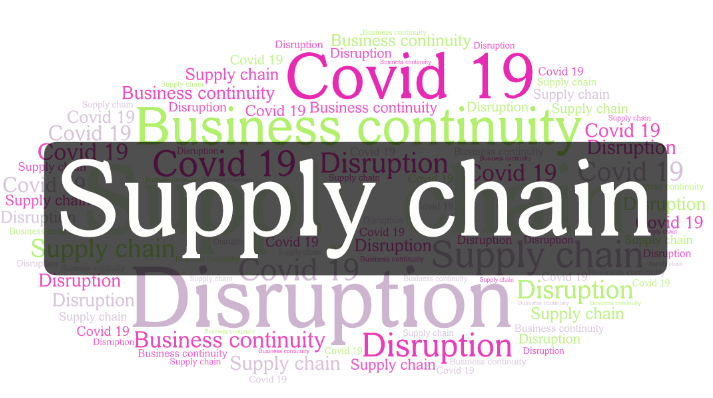
Lock downs in China caused a breakdown in the industrial supply chain globally. Businesses reliant primarily on Chinese suppliers were already impacted early on. Of course as the virus spread, industries in other countries were also forced to shut down regardless of whether they could or could not carry on business.
While we are not saying that businesses should not rely on China for supplies, businesses should look into alternative sources of supply as well as alternate products to ensure business continuity. Each of the SARS outbreaks have resulted in supply outages and disruptions to the logistics networks.
This then comes to the question of buying at low prices and maximizing profits.
However, if it was possible to even out the cost, buy some at low, some at medium prices, from different sources, then the business would be able to avert the possibility of not having any supply at all.
The ability to provide alternate products if a supply runs out would ensure some degree of business continuity.
As with the current situation where hand sanitizers, face masks, disinfectants, etc were sold out and you could not find them in pharmacies.
The businesses that had alternate products were able to supply these to meet the spike in demand.
Businesses should therefore look for different sources of supply and alternate products as a hedge against possible future disruptions.
Update – March 2021
Supply chain disruptions can occur at any time, not just during a pandemic like we are experiencing now.
In March 2021, Evergreen’s container ship Ever Given, became wedged in the Suez Canal, effectively blocking one of the world’s busiest trade routes.
Although the blockage was eventually cleared, it is estimated that the incident will have a knock on effect on the supply chain for several months.
Businesses are now looking at “just in case” inventory planning as opposed to “just in time” to mitigate stock outs.
Surviving the coronavirus crisis
- Covid 19 – Communication is key
- Covid 19 – Business continuity
- Covid 19 – Managing cash flow during the crisis
- Covid 19 – Scaling down
- A COVID-19 Survival Guide for SMEs
Other articles
- As a business grows
- Is your accounting software doing enough?
- Managing inventory
- Key benefits of having the right solution to inventory management
- Unified solutions for better management
- Collaborate internally
- Multi Company Management
- Sage Reveals Malaysian Businesses Incur RM56.6 Billion Losses In Productivity A Year
- Mitigating Supply Chain Disruption
- Inventory costing methods
- Sage Wins Two Frost & Sullivan Asia Pacific Awards
- Procure to pay
- Going digital
- What is an ERP system?
- Covid 19 Surviving the coronavirus crisis
- Covid 19 pandemic – Lessons we have learnt